Reading time: 3 minutes
Textiles made from tropical fruit – sounds familiar? Indeed: at the Trend Space during Heimtextil 2024, Re-Root-Tex unveiled its textile innovation made from pineapple leaves. The filling for the new quilt comes directly from Re-Root-Tex. Their motto? Upcycling over recycling! Here's a look at the joint project.
The quilt from Kauffmann is aimed at an audience that values sustainability and comfort. The textile innovation is to be found in the filling, which is made from the leaves of the pineapple plant. The supplier of this innovative filling is Re-Root-Tex, a start-up dedicated to developing pineapple-based ecological textile solutions suitable for industrial use.
What makes this innovative fibre so extraordinary is that it is sustainable in multiple ways: the plant is not grown specifically for fibre production. Instead, the leaves are a by-product that would otherwise be incinerated or disposed of. In this way, Re-Root-Tex reduces general raw-material usage, the amount of waste in the food industry and the emission of CO2 and methane gas that would be generated by conventional disposal through fermentation or incineration. Moreover, the purely mechanical process completely dispenses with chemical additives – a unique selling proposition.
Re-Root-Tex is based on research carried out by the company's founder, Rony Khan, as part of his doctoral thesis. We spoke to Rony Khan.
When and how did you come up with the idea of making textiles from pineapple waste?
Rony Khan: My original background is in the traditional fashion sector. The initial impulse to rethink came in 2020 during the Covid pandemic when the skies suddenly became completely clear due to the flight ban. Being made so clearly aware of the fatal consequences of our actions triggered something in me so I began to look for an alternative way to make textiles that would help people and not harm the earth.
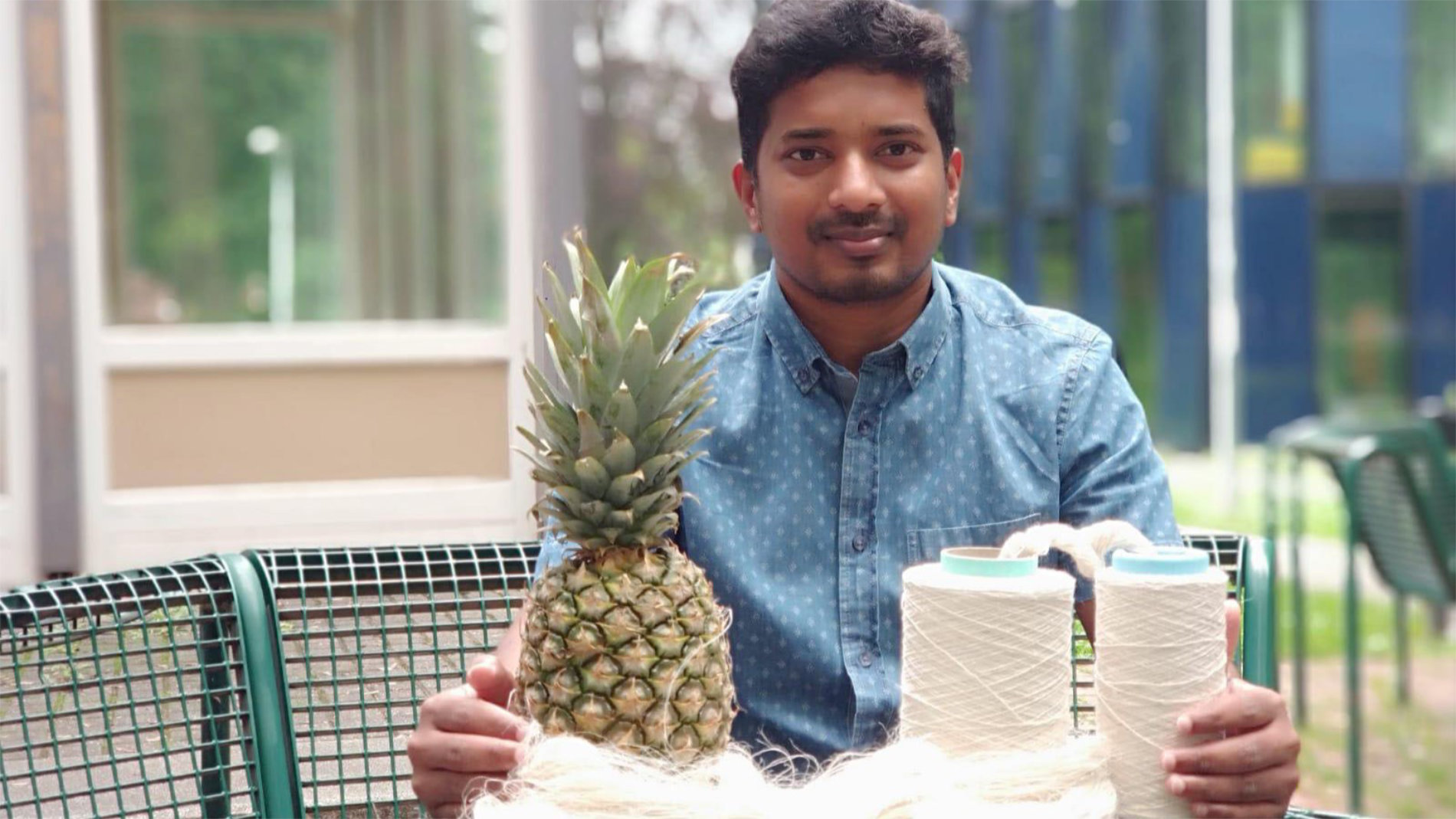
How did you get into pineapples?
Rony Khan: It's actually quite simple: I grew up on a farm in Bangladesh. There I saw the masses of organic waste that are produced during the harvest – in other words, the huge volume of valuable raw materials that could be utilised there.
How does your process work?
Rony Khan: The process itself is not new: particularly high-quality textiles have traditionally been made from pineapples in Bangladesh and in the Philippines. The original production process is highly labour intensive. The fibres are extracted by hand from the leaves, which are then spun and woven. Beautiful but too expensive. To turn this into a marketable product, it was necessary to have a machine that would make this textile solution industrially viable and scalable. I dedicated my doctoral thesis to this goal under the supervision of Prof. Maike Rabe at Hochschule Niederrhein (University of Applied Sciences). Naturally, I stayed true to the principle: the process still works purely mechanically, with absolutely no chemicals and minimal water consumption.
How long did this development process take?
Rony Khan: It took about two years until the mechanical process was fully developed. I designed the machines with my partners in Bangladesh. We had to rebuild or adapt them seven times. I also spent around two years working on the quality and marketability of the fibres.
Sanders-Kauffmann presented the new pineapple quilt at Heimtextil 2025. How did the partnership come about?
Rony Khan: There was a stroke of luck involved here: Sanders-Kauffmann was looking for a sustainable alternative to the classic feather filling and had contacted the University of Applied Sciences, among others. By this time, I had noticed that my fibre could be used very flexibly. When I applied for the project, I was able to present the first concrete results, which were convincing.
How long did the development for the filling made of pineapple take?
Rony Khan: Sanders-Kauffmann was involved right from the start and the partnership for the development of the filling was highly efficient. It took from 2022 to the launch in 2025 because, as mentioned above, I had to work at two locations: in Bangladesh for the machines and in Germany for the fibre properties. But it was worth it, and I am very happy with the excellent result.
What other fields of application do you have in mind?
Rony Khan: In principle, the fibres can meet almost all requirements. The single jersey for the fashion industry, for example, a 50/50 blend with GOTs organic cotton, has been on the market since 2024. Sanders-Kauffmann presented their duvet at Heimtextil 2025. Also, at Heimtextil, our partner Feroze 1888 Mill made its debut with the new collection of towels made from pineapple fibres. Our first T-shirt came with sustainable fashion brand Hessnatur. We are now launching our Ananas Denim with some conscious fashion brands. On top, we received official confirmation in April that our fibre has the best antimicrobial and deodorising properties of all natural fibres. In a nutshell: there is great interest – and we can deliver! All of which represents solid ground for optimism.