Reading time: 4 minutes
In our ‘How things can work’ series, this time we present two exciting newcomers that are currently reaching industrial maturity. In the first part, we start with the French start-up Ever Dye. In part two, we will be talking to British innovator Colorifix.
Time is running out: around 20 percent of global industrial water pollution still comes from the textile industry, much of it from harmful and inefficient dyeing processes. The good news is that acting out of necessity is increasingly becoming a virtue that pays off. More and more organic dyeing processes are not only solving the environmental problem, but also providing tangible solutions to challenges such as rising energy costs and uncertain supply chains. In this way, sustainable dyeing processes are increasingly becoming a tangible economic factor for textile processing companies.
Ever Dye: Magnetising colours
Ever Dye has developed a process that enables sustainable dyeing of textiles at room temperature. The technology offers several advantages: it does not use any petrochemicals, requires around ten times less energy than conventional methods and is five times faster. It can also be integrated into existing production facilities without major changes and therefore quickly demonstrates its efficiency. Ever Dye was founded in 2021 by Amira Erokh near Paris. Today, the start-up works with brands such as Adore Me, Lacoste and Petit Bateau, among others.
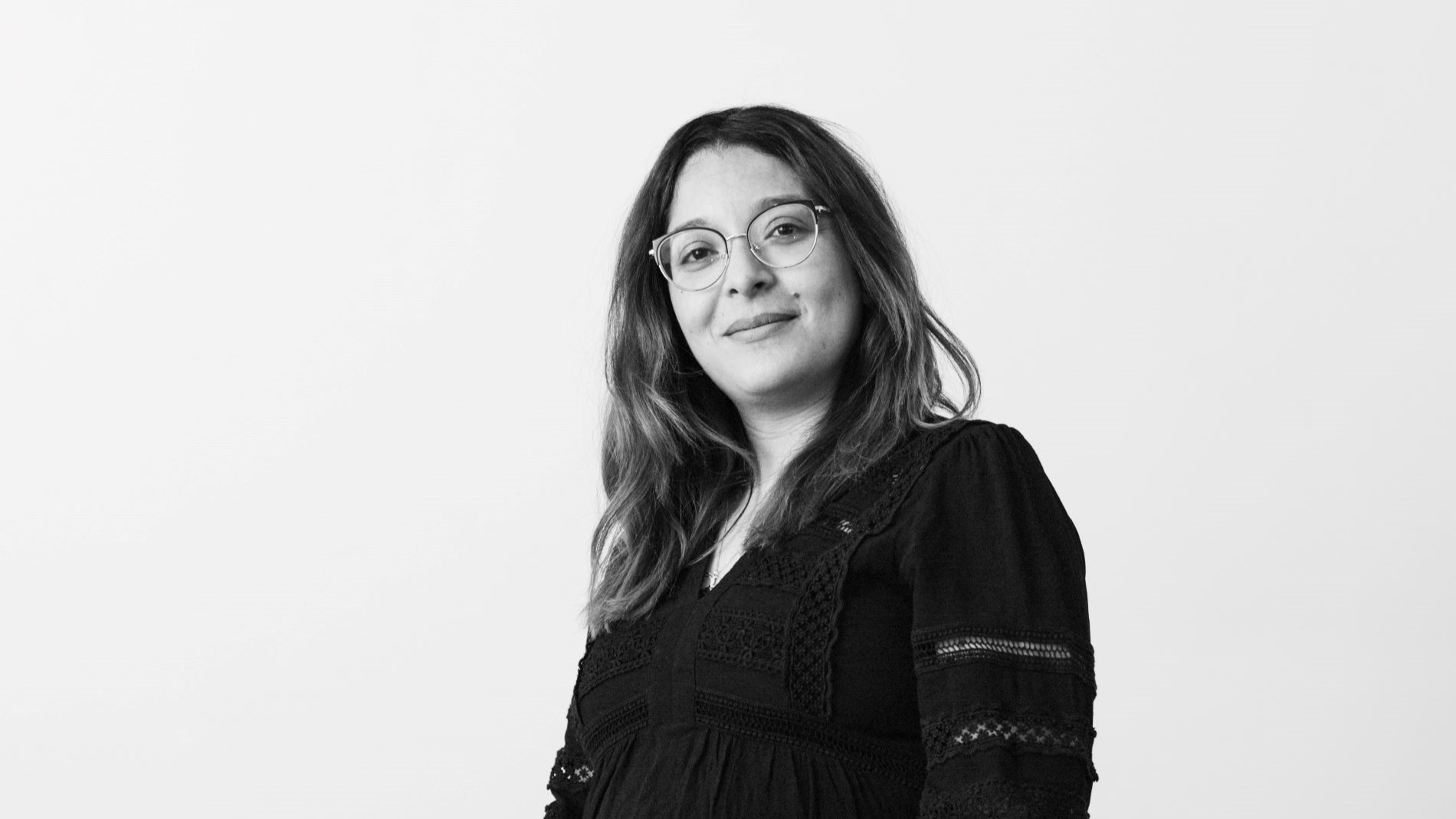
Amira Erokh, PhD, CTO and co-founder of Ever Dye, explains why the ROI for this technology is faster than expected.
Your colours are literally magnetic. How long did it take to develop them?
We actually moved pretty quickly, going from proof of concept to market readiness today. After our launch in 2021, we were able to file our patents in Brazil, Canada, China, India, Japan, Europe and the US in early 2022, and produced the first 100ml pigment samples and dyed fabrics in the same year. In 2023, the first major fashion brands entered the quality development and scalability phase, and since 2024 we have been able to launch a first capsule collection at industrial scale.
How does your process work in detail?
Our technology solves two problems at once: the synthesis and binding of the dyes. We achieve this with an optimal ecological footprint, as we do not use any petroleum-based dyes. Instead, we extract the pigments from organic and inorganic natural elements, which makes the dye completely non-toxic. The trick of our process is the combination of the pigments with a bio-based organic polymer binder. This enables perfect electrostatic bonding – without the use of heat and in a very short time. In practice, the process takes place in two steps: The pre-treatment acts on the surface of the fibre. There it creates negatively charged anchoring points to which the positively charged colour pigments permanently adhere during the actual dyeing process.
Can you produce all colour shades with your process?
In theory, yes, but we're not there yet. We've managed to develop a new, groundbreaking technology in just four years. That's pretty amazing. The colours brown, orange and yellow are ready for the market and meet all quality standards. The Adore Me collection shows just how well these colours work. Next up is a very beautiful blue, which we've almost finished.
The textile industry is extremely cost-sensitive. How does your process pay off for companies?
The dye itself is still slightly more expensive than conventional products, but this difference is almost completely offset. We achieve the greatest positive effect in the dyeing process itself, as the cost-intensive high-temperature heating is completely eliminated. Practical experience shows that companies using our process save around 75 to 95 percent of their energy costs. In addition, the post-treatment requires around 30 percent less water and also simplifies its treatment immensely. The solution is non-toxic, so a simple mechanical filter is sufficient to return the water cleanly to the ecosystem. How quickly the ROI will be realised can be calculated if we continue to scale up and energy prices and climate levies rise at the same time.
There are always pioneers and those who are hesitant. How is the market responding to your innovation?
The response is actually very good. I think companies will have to do something one way or another, and our solution has the advantage of being extremely low-threshold: Ever Dye runs on all existing equipment, which means that in principle no investment is required. And of course, it helps when major international fashion brands demonstrate their commitment. That generates a lot of interest.
Summing up
The tide is turning. Until a few years ago, sustainable dyeing processes still had a few drawbacks – high prices, compromises in quality, etc. – but today, companies such as Ever Dye are impressing with sustainable innovations that are not only low-threshold but also quickly pay off for textile processing companies. It is therefore worth keeping a close eye on developments in the market. In part 2 of this article, we will therefore introduce another player: Colorifix.
Series: How things can work
About the series
The challenges facing companies in the textile industry are multifaceted and, to put it mildly, not without difficulty. They range from rising costs for raw materials and energy, a shortage of skilled workers and supply chain problems to the megatrends of sustainability and digitalisation.
Innovative companies seize their opportunities and take advantage of such challenges to generate their business models. However, this rarely works in isolation. Business and research networks are called for.
In the ‘How things can work’ series, we present companies, start-ups and market leaders that have not only tackled a problem but have also used it to develop a sustainable business venture.
Other articles in the series:
Biological dyes as a key economic factor (Part 2)
The circular economy is not just a passing fad
One for all. Making the circular economy work. (Part 1)