Reading time: 6 minutes
Textile recycling is facing major challenges in its quest for sustainable change: rising volumes of waste from fast fashion, shrinking export markets for second-hand articles, an inadequate recycling infrastructure and new regulations, such as the EU's mandatory separate collection beginning in 2025, are demanding new solutions. One of the biggest hurdles is the efficient pre-sorting of used textiles. Mixed textiles containing different fibres represent a particularly great challenge to high-quality recycling. To overcome these and other challenges, sorting equipment manufacturers have been turning to automation, robotics and artificial intelligence (AI) for some time now.
1. Automatic textile sorting with the aid of algorithms
One such company is Germany's SOEX. The company has been active in the field of collecting, sorting and recycling textiles since 1977, and is one of the pioneers of textile recycling. SOEX has been developing automated technology for sorting textiles since 2015.
“The ability to sort textiles automatically by material and colour...
“The ability to sort textiles automatically by material and colour is an important step towards being able to recycle used textiles to a high standard in the future,” says Vittoria Troppenz, Head of Circularity at SOEX. According to Troppenz, it was foreseeable even back then that the volume of textile waste would increase, and that automated sorting would become more important, especially for textiles that were no longer wearable.
SOEX uses a combination of three technologies to improve textile-waste sorting: near-infrared spectroscopy (NIR) analyses the molecular composition of the textiles and checks whether they are single-origin or mixed textiles, such as polyester/cotton or acrylic/cotton. Then, an RGB sensor sorts the textiles by colour, while an object recognition system – still under development – separates them into different product groups, such as trousers, T-shirts or dresses.
To ensure precise material recognition, SOEX has trained an algorithm based on machine learning, which, according to Troppenz, has a recognition accuracy of up to 95 percent. “Our system can distinguish between 90 different natural and synthetic materials and material combinations,” she says. Currently, the system processes 1,500 items or around 500 kilograms per hour for chemical or mechanical recycling. In addition to textiles from classic container collections, SOEX also processes textiles from the retail sector via its subsidiary I:Collect. These textiles include garments, home textiles, such as bed linen and towels, and workwear. Troppenz has no doubt that SOEX will continue to rely on its in-house sorting technology despite the provisional insolvency proceedings that were initiated recently: “A change of focus towards high-quality textile-waste recycling is vital for the success of a circular textile economy in the future.”
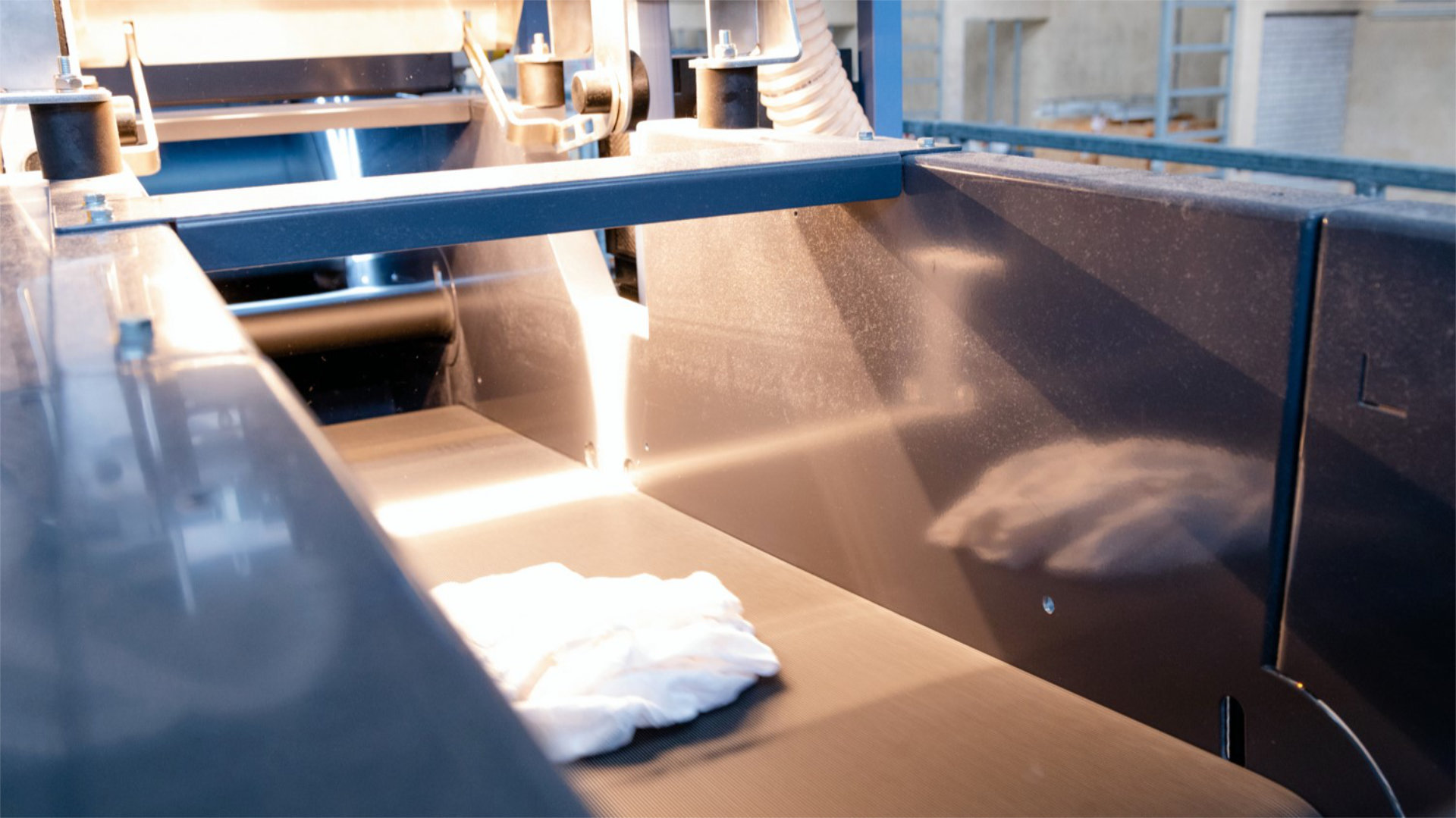
2. Textile-sorting robots
‘NewRetex’, a Danish start-up, is the latest entrant to the textile sorting market. Founded in 2021, the company aims to establish comprehensive new sorting capacities across Europe.
"As a fashion designer, I've worked extensively with cradle-to-cradle concepts"...
"As a fashion designer, I've worked extensively with cradle-to-cradle concepts," explains co-founder Rikke Bech. "The more I learned about the state of circular economy in the fashion industry, the clearer it became to me: Something needs to change." Together with Danish automation specialists, Bech developed a fully automated sorting system for textile waste. While NewRetex employees still open the plastic bags containing unsorted used textiles from municipal collection, robots then take over, scanning and sorting the textiles.
3. Improving digital traceability
The heart of the facility is a patent-pending three-sensor system. It uses NIR and AI to sort textile waste according to colour, texture, and material composition. This triple system is complemented by ‘Huginn’ a tracking tool, the importance of which Bech emphasises:
"The traceability of textile waste is crucial...
"The traceability of textile waste is crucial for successful fibre-to-fibre recycling." Bech is convinced there is no comprehensive textile-recycling system in Europe because sorting isn't standardised, and traceability is virtually non-existent. Accordingly, Huginn documents the journey of used textiles from receipt to the handover to recycling partners, automatically generates sorting reports and, according to NewRetex, can even be integrated into existing ERP systems and external product passport databases. "We owe our Global Recycled Standard certification to Huginn," says Bech.
Mandatory separate collection drives sorting innovation
After sorting, the used textiles are compressed into bales and shipped to recycling partners across Europe. With the facility currently able to handle 1,500 tonnes of used textiles annually, NewRetex also responded to Denmark's separate collection regulation, which came into force in 2023. This regulation requires textile waste to be collected and disposed of separately. "The resulting increase in volumes has heightened the need for automated sorting solutions, as textile waste was often simply exported or incinerated in the past," explains Bech. With the EU-wide separate collection obligation coming into effect in 2025, NewRetex plans to export its sorting technology to support the introduction of a comprehensive textile sorting infrastructure in other European countries.
4. From sorting French fries to AI-powered textile sorting
Work is underway on the future of the textile circular economy in Belgium. With Fibersort, technology company Valvan developed automated material recognition for textiles back in 2011.
"Fibersort was a response to the fast-fashion problem...
"Fibersort was a response to the fast-fashion problem, which leads to large amounts of waste from low-quality clothing", says Jean-François Gryspeert, Sales & Business Developer at Valvan.
According to Gryspeert, Fibersort bridges a gap between textile sorters and recycling companies by identifying the fibre composition of textiles. "With manual sorting, one has to rely on touch and label. However, studies show that label information is incorrect in as many as 50 percent of cases", explains Gryspeert. Fibersort automatically recognises fibre composition – "from baby socks to bed linen". Building on this technology, Valvan developed ‘Trimclean’ in 2020, an AI-aided solution for even better material recognition. Gryspeert vividly recalls the unexpected source of inspiration for Trimclean: "One of our engineers was visiting a nearby company that makes French fries. There, he saw how visual inspection was being used to sort out substandard fries. This led to a brainstorming session on using AI to process visual information when sorting textiles". According to Valvan, Trimclean is now so good that it can even recognise and automatically sort out patches, seams and prints on textiles.
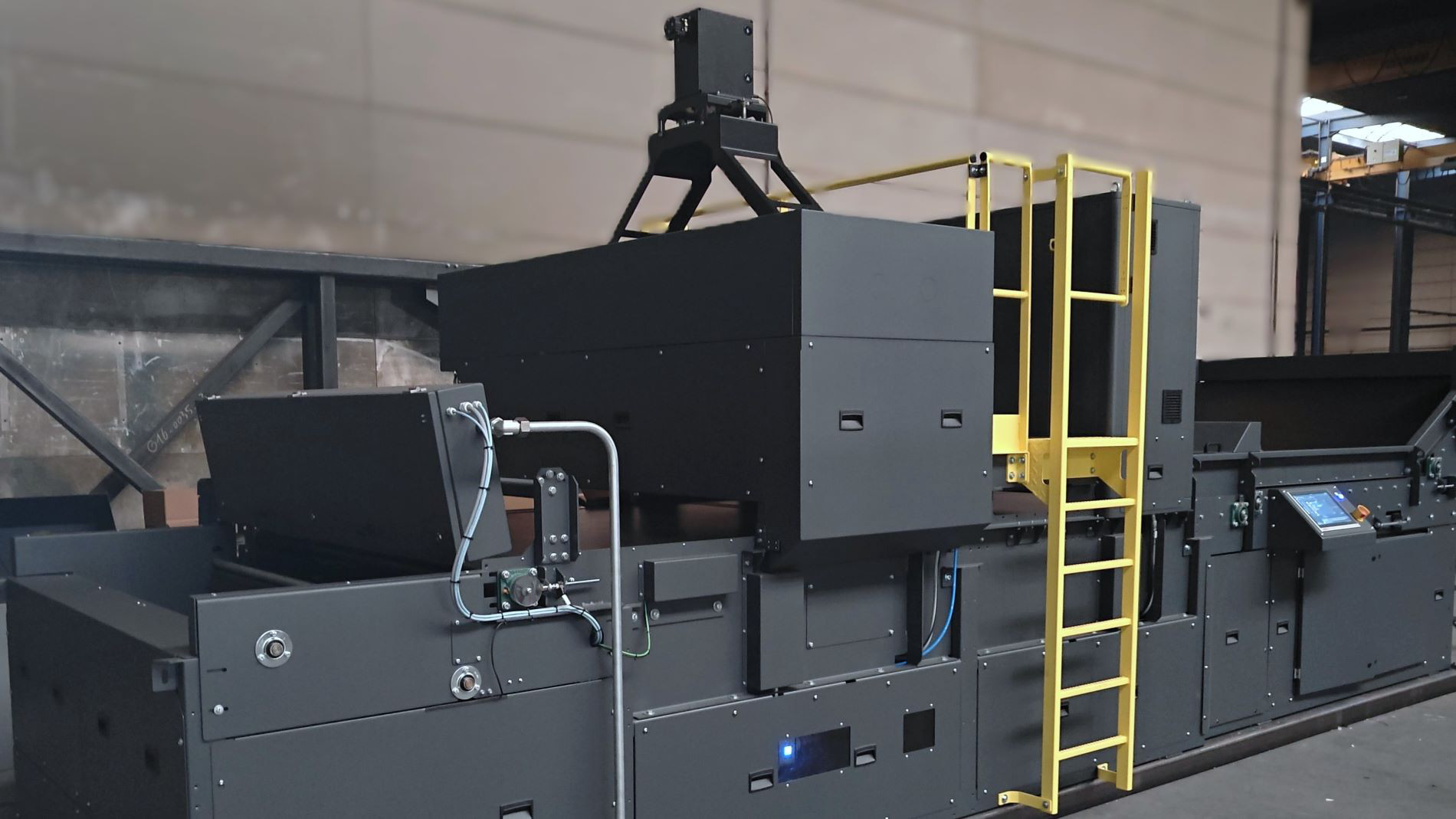
5. "Technically everything is possible. Now we need investment."
According to Gryspeert, the technical challenges in textile recycling have largely been solved. "Technically, everything is possible, especially as chemical recycling gains momentum", he says.
Now investment is called for...
Now investment is called for. "What we need in the coming years is money. EPR, or Extended Producer Responsibility, will become reality in 2025, and success now depends on attracting investors to expand textile recycling", says Gryspeert.
The industry's response to Trimclean winning the Texprocess Innovation Award 2024 in the "Digitalisation and AI" category shows that there is a demand for pioneering solutions in the field of automatic textile sorting: "Since the awards ceremony in April 2024, we have noticed a significant increase in interest in Trimclean", says Gryspeert. "Almost all the enquiries we receive mention the Innovation Award".
Cover picture: The SOEX system automatically sorts textiles by material and colour and will also be able to differentiate between product types such as T-shirts, trousers and dresses in the future.
Cover picture: The SOEX system automatically sorts textiles according to material and colour and will also be able to differentiate between product types such as T-shirts, trousers and dresses in the future.