Reading time: 4 minutes
Wouldn't it be practical if you could pop your smartphone into your jacket pocket and take it out again fully charged? With thermoelectric fibres, this and much else is conceivable. Hence, a research group at Chalmers University of Technology in Gothenburg, Sweden, has been studying the smart fabric and come up with far-reaching conclusions for the textile industry.
“Smart textiles could be used to power wearables using the body's own energy,” says Professor Christian Müller, Professor of Polymer Science at the Technical University. However, there are other, more effective solutions for this application because the fibres are not highly conductive. Which means the surface area of the material must be correspondingly large if a lot of energy is required and, given the current stage of research, you would theoretically need the surface area of a sleeping bag to make a light bulb glow. In view of this, smart fibres are of particular interest for electronic devices that require little energy but are difficult to connect to a power supply, such as sensors or RFID chips. “This means that there are many more potential applications for smart yarns in the Internet of Things and healthcare,” explains Christian Müller.
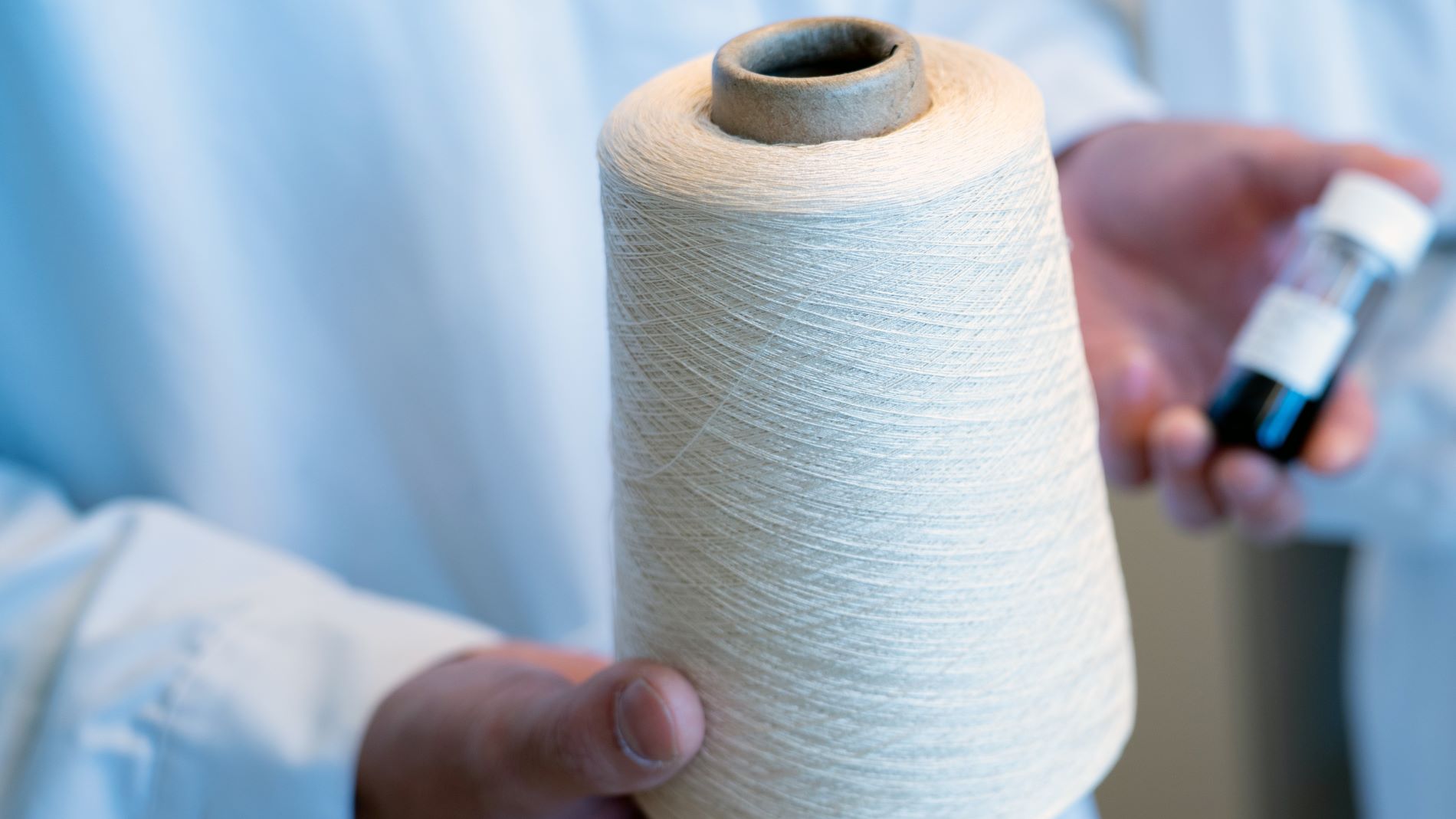
The super fibre
Conductive fibres have been the subject of research for some time now. Previously, metallic components were required to make fibres conductive. However, such components make the fibres inflexible and are neither water-resistant nor environmentally friendly. The breakthrough was made possible by a polymer discovered around two years ago: Poly(benzodifurandione), or PBFDO for short. Based on carbon, it can conduct electricity without any metallic additives, which has many advantages: “The polymer can be worn on the skin in the form of a textile. No rare earth metals are required to make it, and it is also washable,” adds Christian Müller. The scientist is also pleased about something else: materials based on carbon are generally not very durable. “The fibre really surprised us in this respect because it is highly stable,” says Müller.
The core of the super fibre consists of natural silk. The polymer adheres to the outside of the fibre like a dye and, because the surface of the silk is positively charged at lower pH values and the polymer is negatively charged, the two materials combine.
But how does the smart fibre become conductive? Through a process called thermoelectrics whereby an electric current is generated when the fibre encounters a very warm environment on one side – for example, body heat – and a cold environment on the other side. When the electrons in the polymer move from the warm side to the cooler side, the result is a voltage difference – the so-called Seebeck effect, a physical process that was discovered over 200 years ago by Thomas Johann Seebeck.
Under laboratory conditions, a prototype generator was able to produce a voltage of around six millivolts with a temperature difference of 30° Celsius. However, the fibre would be less functional if a person with a body temperature of 37° Celsius were in an environment where the temperature is 37° Celsius.
Material with a far-reaching impact
Christian Müller expects the smart textile to offer major benefits in the fields of medicine and geriatric care. Sensors for medical monitoring could be worn as a plaster, an item of clothing or a wristband – allowing patients to leave hospital earlier. Permanent monitoring of vital data or movements is also conceivable for the chronically ill or the elderly. However, the potential of this pioneering research is much more far-reaching because these smart fibres consist of semiconductors, which are at the heart of almost all modern electronic devices used almost everywhere from consumer goods, industry and the automotive sector to power grids and other infrastructures. Currently, there are only a few carbon-based semiconductors in use, for example light-emitting diodes (OLEDs) and flexible displays.
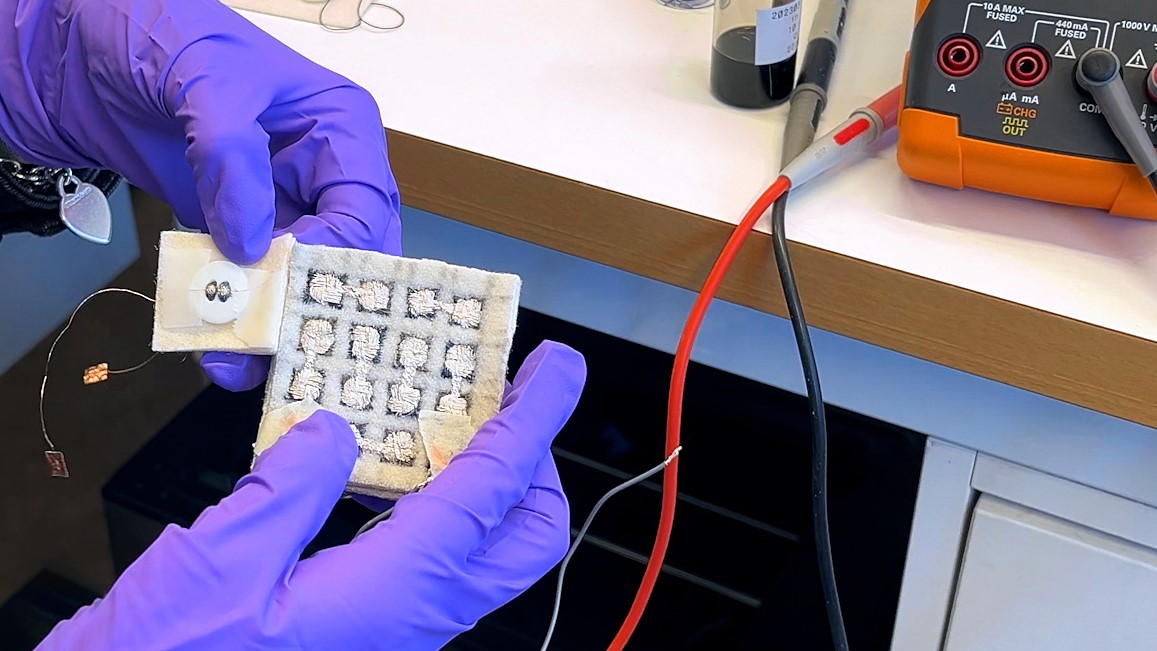
“Our aim is to develop electronic components using organic chemistry, which makes production less complex, consumes less energy and makes the electrical components more cost-effective. Moreover, such components are easier to recycle,” says Christian Müller, “However, the organic materials must be sufficiently robust to permit this.” The smart silk fibre is an important first step in this direction. Previously, thermoelectrics were regarded as a niche technology on account of their low level of efficiency and high production costs. However, thermoelectrics are increasingly becoming the focus of scientific attention as a sustainable source of energy and – as in the case of this research project – are funded by the European Union.
Recycling
The fibre manufacturing process is not particularly complicated and thus requires little energy, which has a positive effect on tomorrow's ecological balance sheet. However, the end of the life cycle has yet to be researched and harbours its own challenges. “Recycling is a very important issue, especially in the textile industry,” says the Professor of Polymer Science, “And this means recycling must be built into the fibre right from the outset. For successful recycling, it is essential that the polymer can be completely removed from the fibre. Given that this plastic is a very recent invention, we don't know its decomposition properties yet. However, in Sweden alone, there are already several research groups working on finding this out. Our goal is to completely recover the silk and reuse the polymer, too.”
The conductive fabric is still undergoing research. Although the EU-funded project is complete, there is still a long way to go before the fabric is ready for mass production. Nevertheless, much has already been achieved because, in addition to the breakthrough in research, 15 doctoral students have now been trained. And, as highly qualified specialists, they are already passing on their newly acquired knowledge to other universities and the industry.
Professor Christian Müller
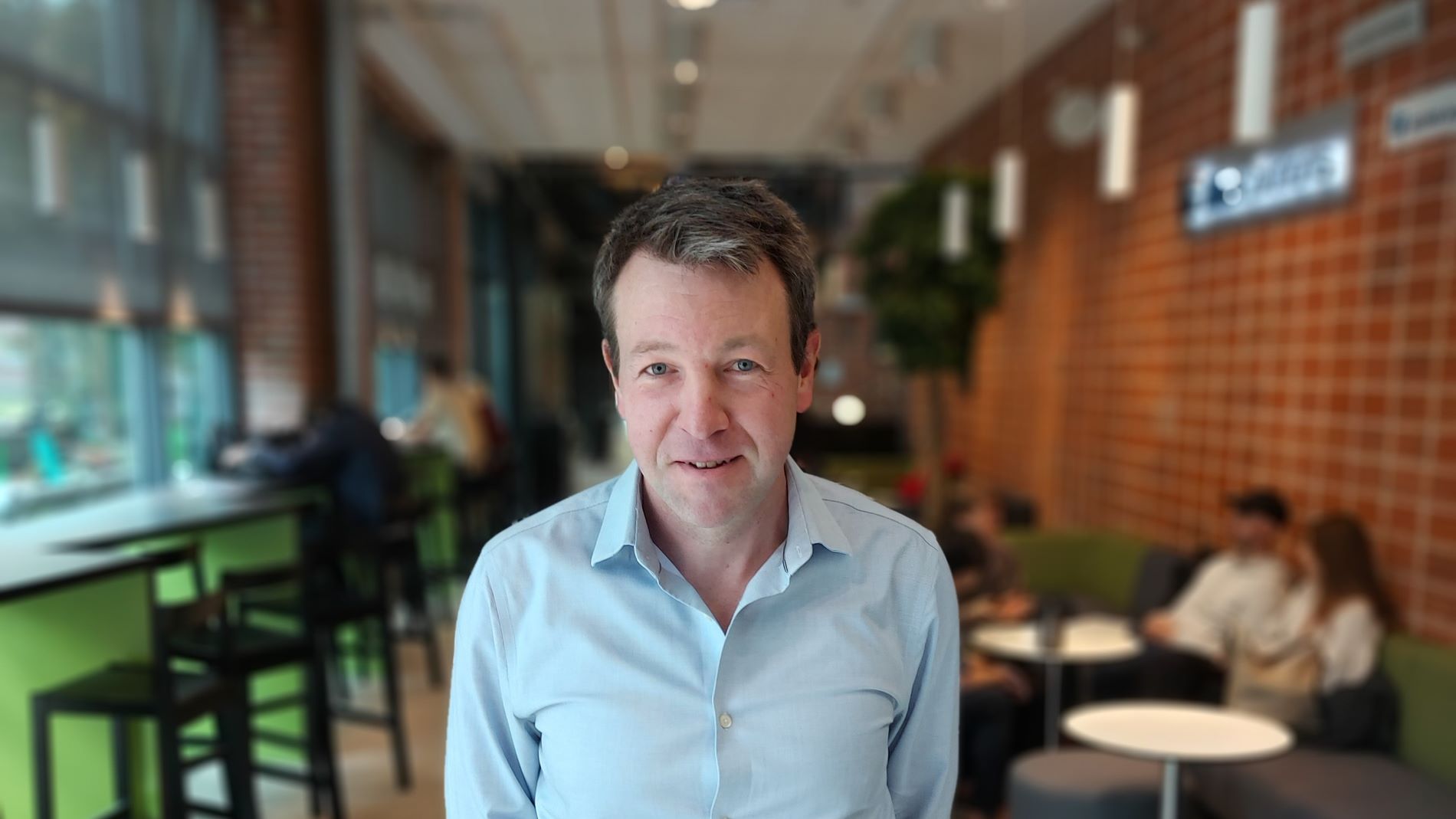
The Professor of Applied Chemistry at Chalmers University of Technology in Gothenburg, Sweden, worked with a team of 15 doctoral students on the ‘Poly(benzodifurandione) Coated Silk Yarn for Thermoelectric Textiles’ research project.