Aigle Macchine S.r.l.
Address
Aigle Macchine S.r.l.
Via Donatello 8
10071 Borgaro Torinese Torino
Italien
Telephone+39 011 262 4382
Fax+39 011 262 4348
Discover more from us
Follow us on
About us
AIGLE began its activities in 1958 building machinery for the flocking of each type of application. During its first decade, AIGLE contributed greatly in developing the technology of flocking, with particular reference to its application in the textile industry. In 1968, AIGLE began undertaking the production of coating and lamination machinery which was considered as natural evolution from the previous products.
Today, after more than 60 years of design, AIGLE produce and sell its machines worldwide. AIGLE can definitely be considered as a partner for the development of new projects, through the provision of solutions for customers who require elements of customisation and specific technical requirements.
All the plants and the machines are designed and produced in AIGLE’s factory which is located in Borgaro Torinese, Italy.
AIGLE’s organisation consists of:
- An engineering department for mechanic, electric, pneumatic, thermic and hydraulic design, which is fully equipped for the industrial design of the plants and machinery with a 3D CAD system.
- A production department equipped with modern tools and instruments along with a prestigious carpentry sub-section.
- An electric/electronic department for studying and creating the control panels and PLC programming required per each plant (they also provide a manual for the wiring).
- Technical and technological assistance for erecting and commissioning the equipment as this is considered a crucial part in the selling process of AIGLE’s industrial culture.
AIGLE heavily invests in research and development, specifically for updating and increasing the level of performance of their FLOCKING, COATING and LAMINATION plants, counting on a qualified technical team for the construction, as well as for the design of the plants and individual machines. The result of these efforts is the installation of machines that allow our customers to cope with the challenges of an increasingly demanding market.
In over 60 years of business, AIGLE has accumulated a vast experience in handling relationships with customers. AIGLE can offer ready and substantiated technical solutions to customers with precise and defined needs and technical requests; but AIGLE can also be considered a partner for developing new projects to face the ever more demanding and complicated market requests.
AIGLE’s main plants list:
- Plants for rubber profile extrusion and flocking, for the rubber profile for the automotive industry.
- Plants for the production of synthetic leather, for use in upholstery, garments and automotive.
- Plants for the finishing of fabrics, by direct and foam coating and printing (traditional and digital), for use in upholstery, curtains, garments and automotive.
- Plants for the production of abrasive paper.
- Plants for the finishing of wall paper, flocking, PVC coating and embossing.
- Plants for the back coating of carpets and synthetic grass with latex and PU.
- Plants for the laminating of fabrics through wet process, powder scattering, hot melt and flame.
- Plants for manufacturing and finishing, by thermo-bonding non-woven for geotextiles.
- Plants for manufacturing and finishing non-woven fabrics for house cleaning.
- Plants for finishing with flock injection moulded ABS and PP for automotive and children’s toys by manual and/or robotised technology.
- Plants for finishing by printing (UV, PVC, pigments etc.), flocking and glittering paper (continuous and in sheet form) for packaging and decoration.
Our product groups
- Produktionsverfahren
- Verarbeitungstechnologie
- Beschichtungsanlagen
- Laminier- und Kaschieranlagen
- Textilveredelung
- Sonstige Maschinen und Geräte
- Technologie, Verfahren, Zubehör: allgemein
- Textile Verbindungssysteme: allgemein
- Membranen: allgemein
- Veredelungs- und Ausrüstungsverfahren
- Laminier- und Beschichtungsstoffe
- Materialvorbehandlung
- Oberflächenveränderungstechniken
- Beflockung
- Bondtec: allgemein
- Neue Ausrüstungen
- Funktionale Bekleidungstechnologien: allgemein
Our application areas / Solutions
More about us
Special Interests
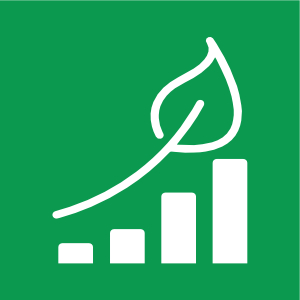
Keywords
- Coating
- Flocking
- Finishing
- Laminating
Our Products
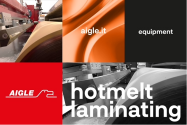
Hotmelt
Application systems for hot-melt lamination lines:
– System with smooth or engraved cylinder
– Slot system.
Aigle collaborates with Bridarolli Srl in the use of hot-melt systems. The combination of these experiences allows us to offer a reliable and consolidated technology that is always oriented towards innovation and research.
Characteristics of these application systems are:
– Smooth cylinder system: it allows the application of an average greater quantity of hot-melt component and can only apply a single uniform layer of adhesive.
– System with engraved cylinder: allows the application of the adhesive in spots, making the coated / coupled material breathable and, therefore, soft.
– Slot system: allows a wide variability of adhesive application grammage: from 2-3 g to 10 g / m2 for non-total coverings or up to 500 gr / m2 for total coverings, with very high application uniformity.
Aigle / Bridarolli Slot system offers the possibility to change of adhesive weight easier than with the classic engraved coating system. There is no need to replace the cylinder or to invest in the purchase of the cylinder itself. The use of Bridarolli Srl melters and extruders ensures proper supply of the hot-melt adhesive to the application device.
The application of adhesive / hot-melt materials in industry are extremely varied:
– Self-adhesive materials: (non-woven/woven fabrics, foams, plastic films etc. can be coated with a self-adhesive hot-melt) these materials are used in the shoe-making industry to produce insulation materials
– Plasticized materials: woven fabrics, used for instance to produce plasticized tablecloths, coated by thermoplastic hot-melts
– Back coating: for upholstery fabrics and for a black-out finish (by coating thermoplastic EVA hot-melts)
– Laminated materials: (non-woven/woven fabrics, foams, plastic films etc.) using both thermoplastic hot-melt adhesives and reactive PUR adhesives produces materials for the upholstery industry to the automotive industry, for example.
Through the engraving roller system, the following items can be produced:
– Dot-coated materials: (non-woven/woven fabrics etc. coated with thermoplastic hot-melts) used as interlinings
– “Network shaped” or dot-coated materials: these materials are coated with thermoplastic hot-melt adhesives and become adhesive when heated at the adhesive melting temperature. They can be used for many different purposes; for example, non-woven fabrics are used to cover the interior surfaces of vehicles
– Breathable but waterproof laminates: used in the garment and shoe industry and is obtained by laminating a membrane to fabrics
– Breathable laminated materials: (non-woven/woven fabrics, foams, plastic films etc.) uses both thermoplastic hot-melt adhesives and reactive PUR adhesives; used in different fields from upholstery to the automotive industry etc.
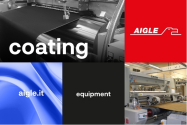
Coating
Coating is an industrial process which consists of the provision of a base (fabric, paper, etc.) and the application on it of a chemical product, then drying through an oven, a possible infrared heating or embossing, cooling and rewind.
The nature of the chemicals involved can be acrylic, polyurethane, silicone, latex, PVC, etc.
The ability to work with different coating techniques is the criterion that has characterized the development and design of our machines. The new techniques used to achieve these standards are the result of years of experience in which AIGLE has created high-tech systems around the world. The ease of use and the wide opportunity to make adjustments and customizations make our coating machinery highly versatile.
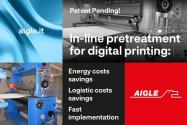
Digital printing
Aigle Macchine Srl has developed and patented a system for pre-treating incoming fabrics of digital printing lines.
The system consists in doctor-blade coating a chemical product (compound for printing with acids or reactive) on a fabric to improve the printing carried out in a digital machine (plotter, discontinuous and continuous feed). The fabric is then pre-dried, calendered and fed onto an adhesive conveyor belt of a digital printing line. The fabric can be pre-dried on the reverse side. For this purpose, there is a heater close to the 'light' squeezing calender to be carried out after coating. The coating system for digital printing fabric pre-treatment is also equipped with a synchronizing unit suitable to compensate the continuous or discontinuous coating feed with the web feed of the printing machine.
Machine is suitable for:
Full cover coating over cylinder
Full cover coating by floating blade
Strengths new pre-treatment bench for digital printing mod. bsr-dig
1) ability to print wet-on-wet for better colour penetration.
2) possibility of increasing or decreasing the degree of wetting of the fabric before printing
3) can be used with all types of colour (acids, reactive pigments)
4) impregnation step with stenter frame oven is avoided
- less use of manpower
- less energy use for the line with stenter frame oven
- less waste of chemistry at the end of processing when washing out the residual unused chemistry
5) sustainability.
- less use of water in the case of use of shelter (reagents).
- less use of space for storage of pre-treated pieces waiting to be processed with risk of yellowing and necessary cleaning and reprocessing treatment in case of prolonged shelf waiting.
6) cost-effectiveness:
50 cents (euro) machine passage
- 12 cents raw materials
- 8 miscellaneous expenses squeegee treatment
= savings of about 30 cents per square meter
with a production of 2000 square meters per day = about 130,000 euros per year. payback in about 1.5 years.
7) possibility of making immediate prints without the wait for pre-treatment in the stenter frame oven
8) ability to process all fabrics even the most complex ones like wool and silk.
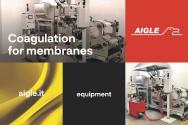
Coagulation
Coagulation lines are used for the production of filters and synthetic leather. This is a wet process. The substrate is first impregnated or squeegeed or slotted and then placed in contact with water diluted with other chemical compounds.
The characteristics of the Coagulation Line – mod. LC/F are as follows:
– The fabric or substrate is twisted through unwinders and in case also accumulators. The accumulator can hold several linear meters of fabric, providing enough time to replace the empty roll with a new one without stopping the coagulation line.
– Also self-aligning pulling units guide the fabric or substrate through the line These units ensure uniform tension of the fabric or substrate.
– Next, alternative coating and/or impregnation routes are taken using various techniques (squeegee, slot, etc.).
– The substrate is then coagulated,
– proceeds to one or more washing tanks with or without wringing calenders.
– Finally, the product is dried and rewound.
Systems for detaching the coagulated membrane from the substrate are also used along the line
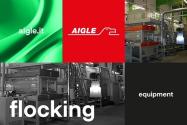
Flocking
Flocking is an industrial process which gives the treated product a velvety and soft effect.
The surface to be treated is coated with a specific adhesive, and subsequently put through an electrostatic system where millions of textile fibres are applied over it.
The flocking ensures that the surfaces treated become special, accumulating new aesthetic features and/or functionalities. For example, non-slip, soundproof, anti-glare, anti-condensate, anti-scratch, etc.
The market sectors where flocking can be applied are many. A few examples are:
– Furniture: blackout curtains, curtains, external sun curtains, tapestry for sofas and beds covers, wallpaper, tablecloths, non-slip materials, etc.
– Clothing: jackets, shirts, pants, accessories, sports & security clothing, etc.
– Objects: (can be applied on plastic, wood, metal, porcelain, glass, foam, etc.) springs, carpets, profiles, hangers, toys, glasses cases, flocked swabs, etc.
AIGLE offers the widest range of flocking machines. The quality, versatility and customisation of its machines make AIGLE the leader of the flocking market. This range is divided into: Flocking Profiles, Flocking Objects, Flocking Fabrics and Roll Materials.
Our Contact Persons
SADUN ALBERTO
Vertrieb
Geschäftsführer*in
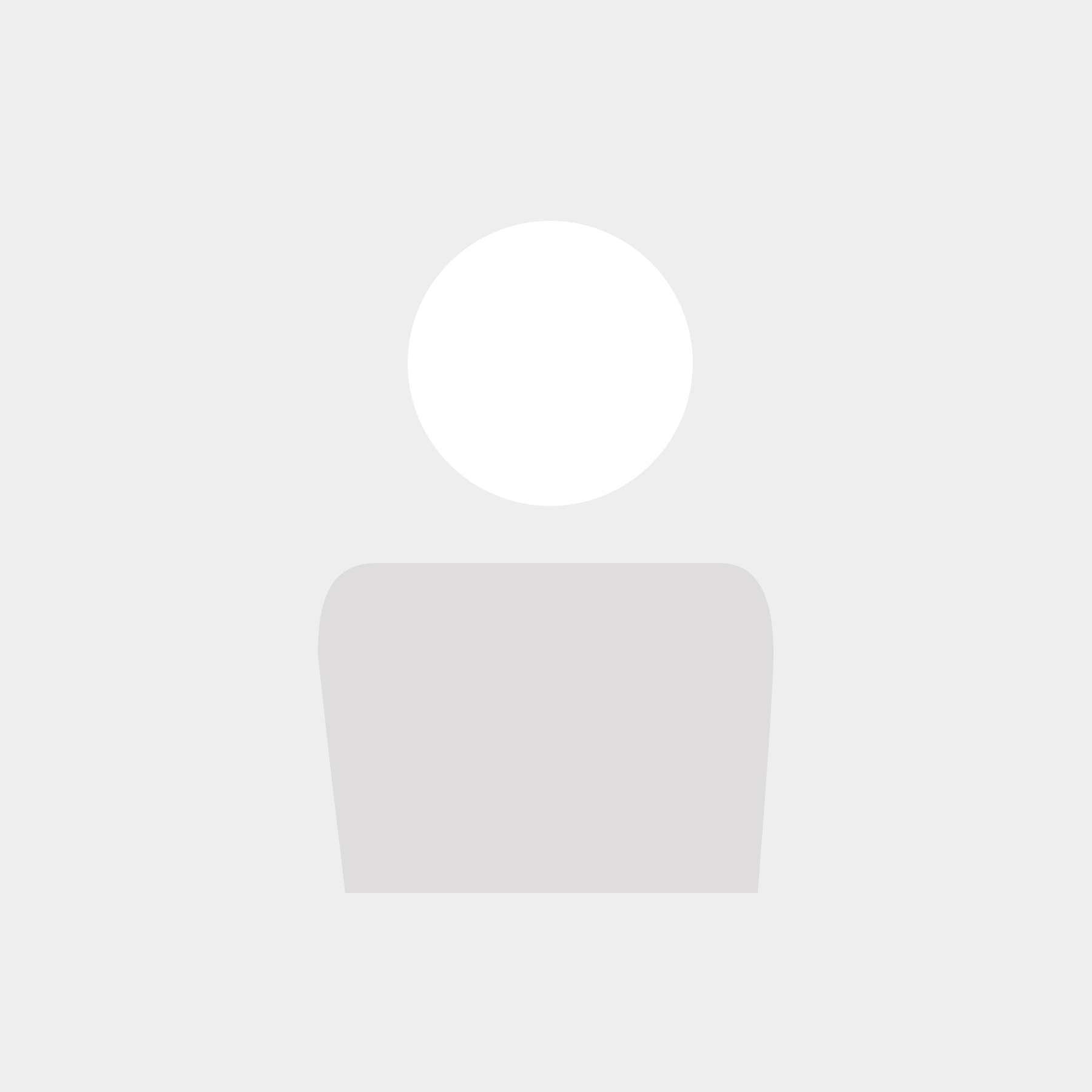