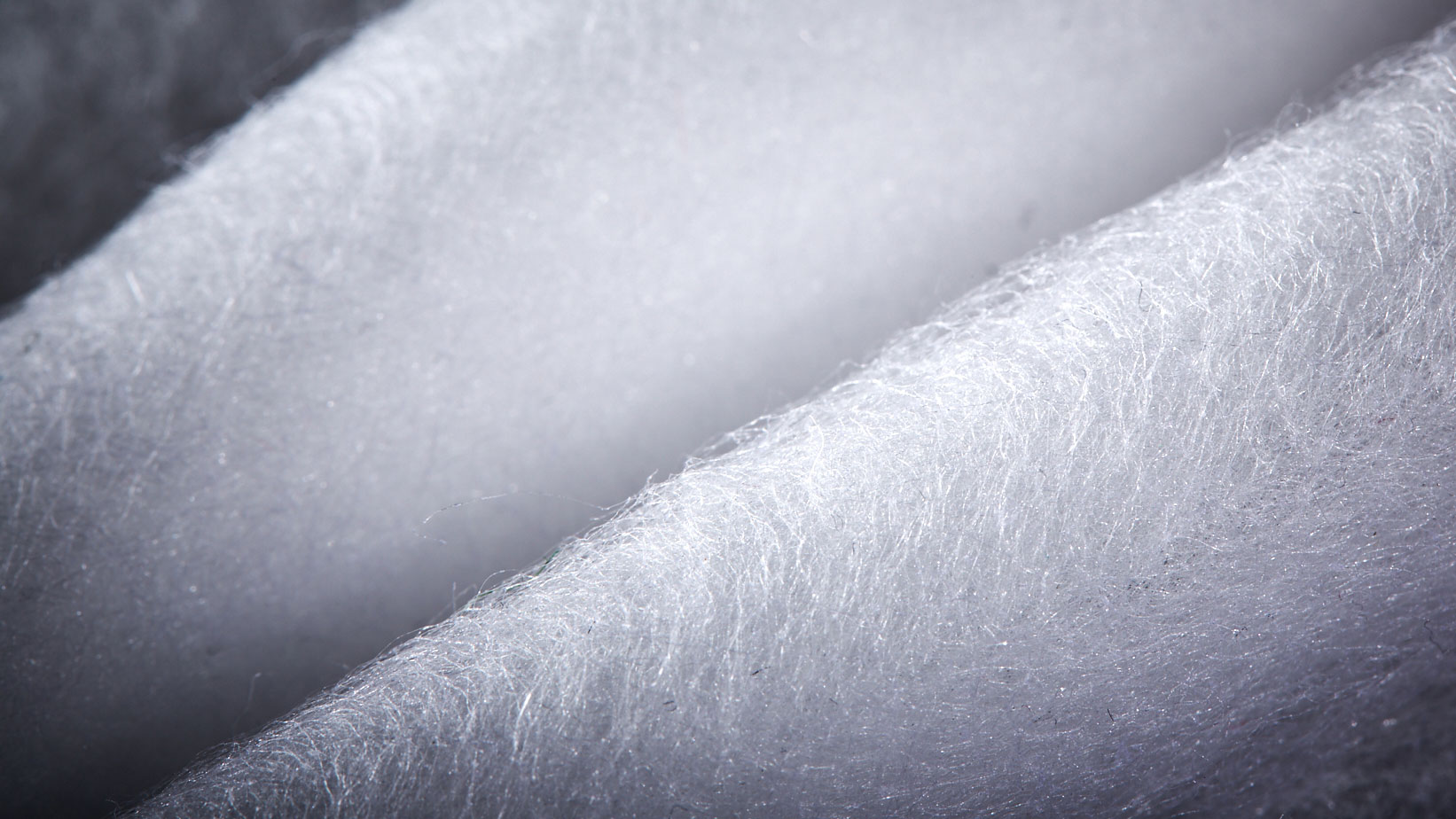
When a cherry tree loses thousands of blossoms in spring, is that waste? Or even environmental pollution? No, it's nature's cycle. The cherry tree thrives on excess and in doing so, it is climate positive and beneficial. Founder of the cradle to cradle model Professor Michael Braungart has long used this example to inspire a rethink in industry.
The mountains of waste are getting bigger and resources are dwindling. If the surplus production of clothing is to continue, something has to change. Polyester, for example, which is found in 69 per cent of all clothing, takes on average 500 years to degrade1. Consumer goods must therefore be manufactured in a way that enables them to be restored to the biological cycle – something which various companies along the textile supply chain are currently working on. Adidas for instance recently introduced Bionic Loop, one of three strategies with which the sporting goods company from Herzogenaurach aims to end plastic waste. With products such as sneakers made from plastic trash recovered from the ocean by Parley for the Oceans, Adidas has been working on solutions for a more sustainable fashion industry for some time. Made to Biodegrade is another component of its End Plastic Waste campaign. One of the first products in this line is an Adidas tennis dress by Stella McCartney. Developed in partnership with fibre manufacturer Bolt Threads, it is made with cellulose blended yarn and Microsilk. Much like spider silk or milk fibre, Microsilk is a protein-based material, made in this case with water, sugar and yeast.
Fibre manufacturer Freudenberg has also made advances in bio-degradability. Comfortemp is a sustainable material for high performance clothing which has excellent insulation values. Comfortemp fibres used to be made from post-consumer PET bottles, but Freudenberg has now developed a biodegradable alternative in partnership with the Austrian company Lenzing. This innovation appeared on the market in January 2020 – Comfortemp Lyocell, a padding made from eucalyptus leaves sourced from sustainable forests. The cellulose fibres degrade fully in soil in 60 days[1] to become part of nature again, fertilizing new resources.
Discover the latest sustainable innovations of exhibitors like Freudenberg and Lenzing at the upcoming edition of Techtextil, the leading trade show for technical textiles.
#Circular economy #Biodegradable #Cradle to cradle #Adidas #Stella McCartney # Parley for the Oceans #Microsilk #Comfortemp Lyocell #Freudenberg #Lenzing #Sustainability #Innovation #Techtextil #Frankfurt am Main
Find out more here:
- https://techtextil.messefrankfurt.com/frankfurt/de/presse.html
- www.facebook.com/techtextil
- www.twitter.com/techtextil
- www.linkedin.com/showcase/techtextil
- www.instagram.com/techtextil_texprocess
- www.techtextil-blog.com#
[1] Freudenberg (2020): https://www.freudenberg-pm.com/Presse/2020_02_Lyocell